Why do industrial sewing machines not use induction motors?
In the world of industrial sewing, choosing the right motor is essential for optimal performance.
Industrial sewing machines often do not use induction motors because they require high precision and control that these motors cannot provide.
Instead, servo motors and clutch motors are preferred for their ability to deliver the speed and accuracy needed for specialized sewing tasks.
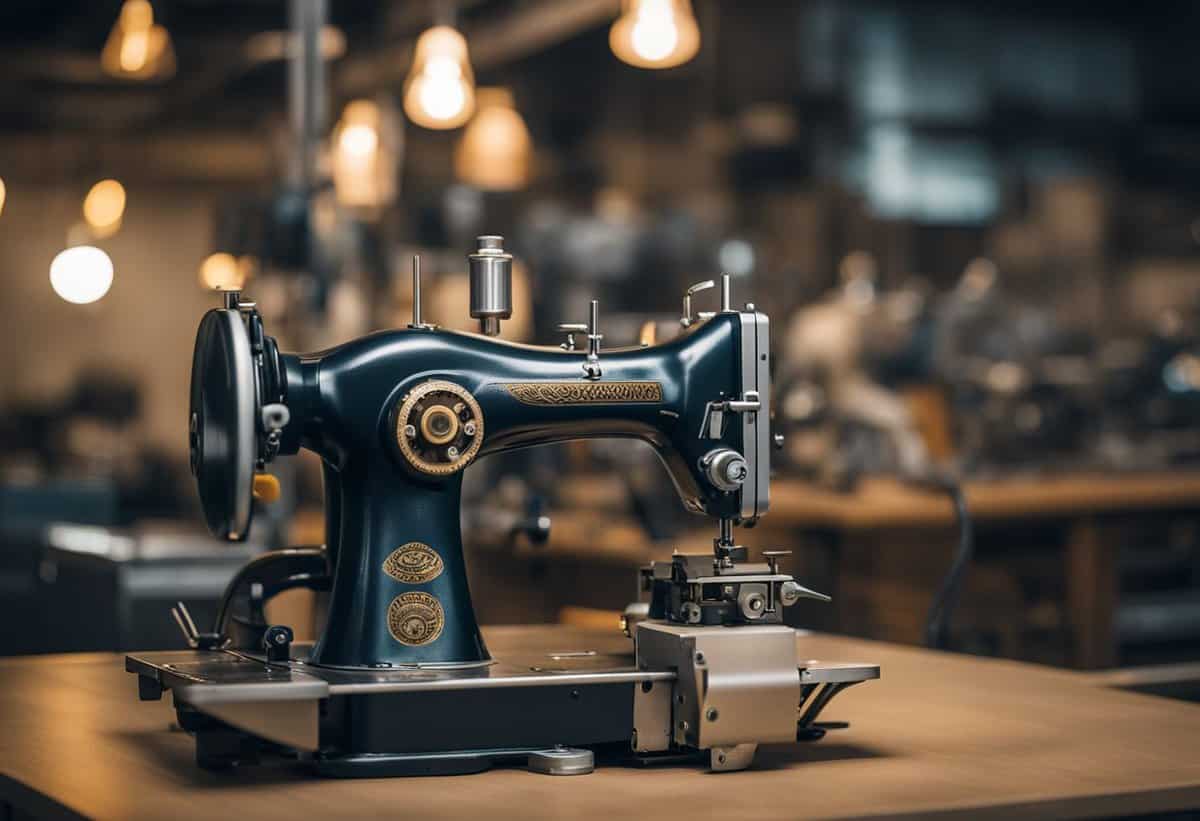
I find it fascinating how the type of motor impacts the efficiency of sewing operations.
Induction motors generally run continuously and can lack the fine control that modern sewing demands.
Hence, servo motors, which operate with feedback systems for precise adjustments, are more suited for the fast-paced and varied tasks in industrial settings.
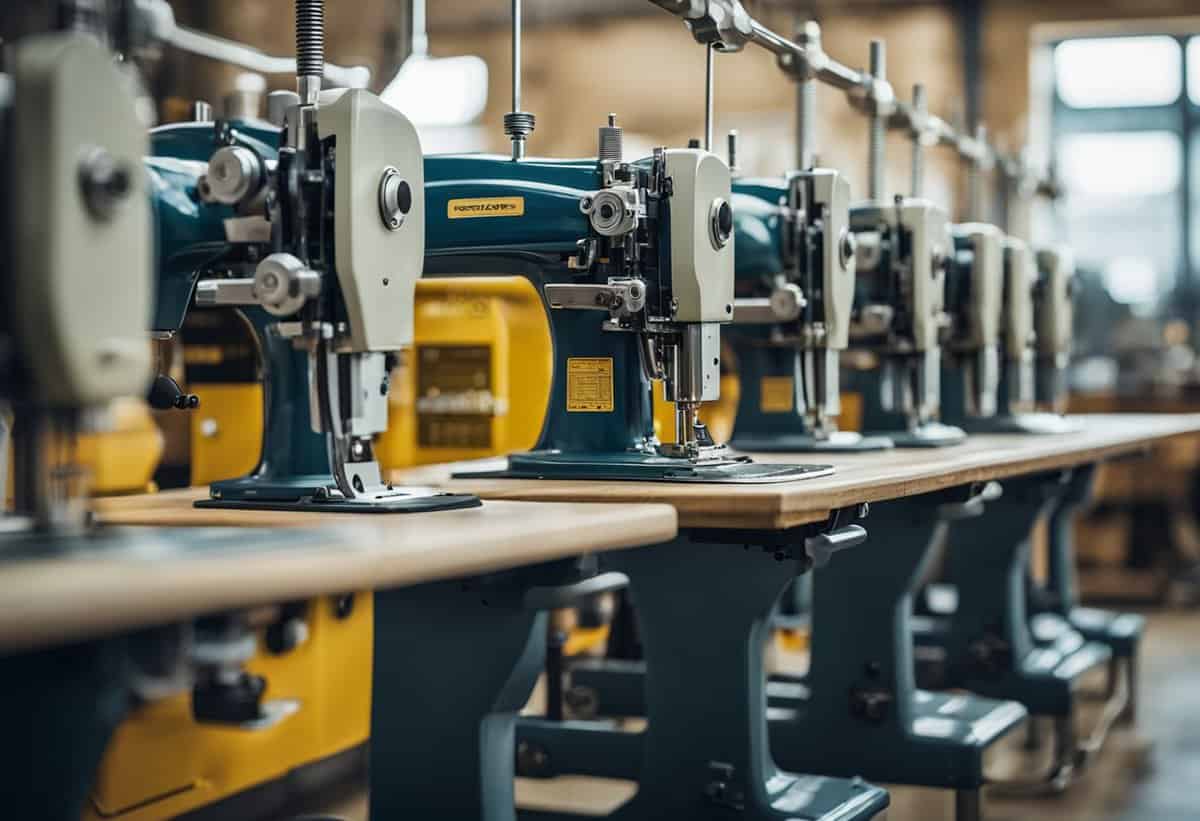
Industrial sewing machines are built for high-speed and heavy-duty operations. They are designed specifically for mass production, making them essential in various industries like fashion and textiles.
These machines have unique functional requirements and commonly use specialized motors that suit their operational needs.
Contents
- 1 Table of Contents
- 2 Understanding Induction Motors
- 3 Mechanical Demands of Sewing Machines
- 4 Electrical Considerations for Sewing Machines
- 5 Comparison with Other Motor Types
- 6 Cost and Maintenance Factors
- 7 Innovation and Future Trends
- 8 FAQs:
- 8.1 Why do industrial sewing machines not use induction motors?
- 8.2 What types of motors are commonly used in industrial sewing machines?
- 8.3 Are induction motors less efficient than servo motors in sewing machines?
- 8.4 What are the key performance factors considered when choosing motors for sewing machines?
- 8.5 Why are induction motors more commonly used in other industrial applications?
- 8.6 Can induction motors ever be used in industrial sewing machines?
Functional Requirements
Industrial sewing machines must perform under rigorous conditions. They need to handle different fabric types and thicknesses while maintaining precision.
Speed is also crucial; many machines can operate at high RPMs to increase productivity.
Each machine is usually set up for specific tasks, such as straight stitching, zig-zag, or overlocking. This specialization allows for consistency in production.
The durability of parts is essential, as industrial machines often work for long hours without breaks, requiring maintenance and strong components to endure frequent use.
Common Motor Types Used
The choice of motor is vital for industrial sewing machines.
- Servo motors and clutch motors are the most common types.
- Servo motors provide precise control and energy efficiency, making them ideal for varied applications. They respond quickly to control changes, which enhances performance.
- Clutch motors, while less energy efficient, offer a direct connection to the machine. They are often used in high-speed settings but can be less flexible in operation.
Induction motors are generally not preferred due to their slower response times and lower efficiency in applications that require frequent speed adjustments. This lack of adaptability can hinder the precise control needed in industrial sewing tasks.
Table of Contents
Understanding Induction Motors
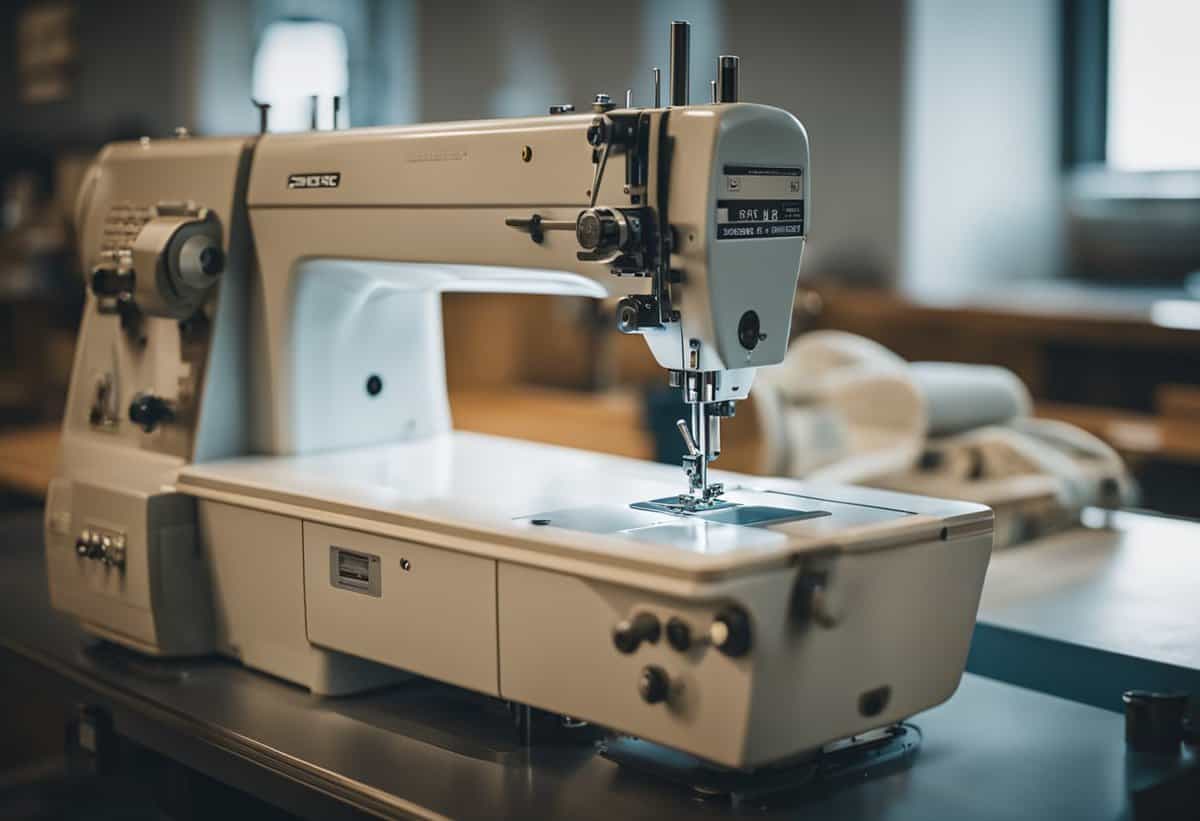
Induction motors are widely used in various industries due to their design and function. They have specific principles of operation that ensure they work efficiently.
Principles of Operation
Induction motors work on the principles of electromagnetic induction. When an alternating current flows through the stator windings, it creates a rotating magnetic field.
This field induces current in the rotor, causing it to turn. The rotor doesn’t have to be connected directly to the power source, like in other types of motors.
The key components include the stator, rotor, and bearings.
Most induction motors operate at a constant speed. They offer simple construction and require less maintenance compared to other motors. This makes them popular in many industrial applications, but their features may limit their use in more sensitive setups like sewing machines.
Advantages and Disadvantages
Induction motors come with several benefits. They are generally robust, cost-effective, and efficient for many uses.
Their construction is simple, which leads to lower manufacturing costs. This makes them attractive for larger operations.
However, they also have downsides. They may not provide the precise speed control needed in applications like industrial sewing machines.
The lower starting torque of induction motors can also be a drawback in environments that require immediate and powerful startup capabilities, making them less suitable than servo or clutch motors in sewing applications.
Mechanical Demands of Sewing Machines
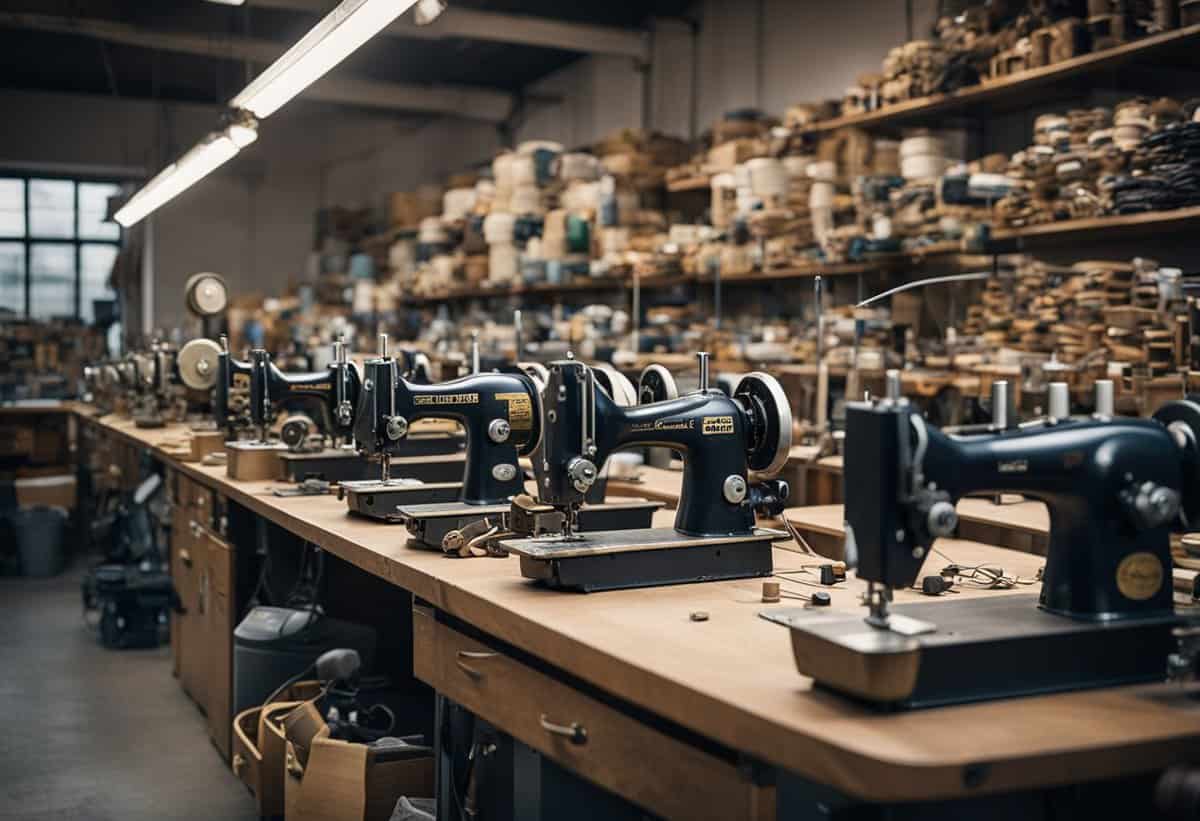
I find that the mechanical needs of sewing machines are quite specific. These machines require precise control, strong torque, and quick responsiveness to handle various sewing tasks effectively.
Speed Control Necessities
In industrial sewing, speed is crucial. Machines often operate at high RPMs, making precise speed control essential.
Using direct drive motors, for example, gives quicker response times compared to induction motors.
Direct drives offer better speed modulation, letting me make fine adjustments seamlessly.
This capacity for instant speed changes helps in handling intricate designs or thicker fabrics without skipping stitches.
Torque Characteristics
Torque is another vital aspect. Industrial sewing machines need high starting torque to handle dense materials.
When the machine begins, it requires enough force to push through the fabric quickly.
DC motors or servo motors excel in this area. They can deliver substantial torque even at low speeds.
This characteristic is essential when starting on heavy fabrics or layers, preventing needle breakage and ensuring smooth performance.
In contrast, induction motors struggle to provide the same level of torque, particularly at low RPMs.
Precision and Responsiveness
Precision is critical in sewing tasks. Industrial machines must respond rapidly to changes to maintain consistent quality.
The capability to start, stop, or reverse quickly is key in creating complex designs or matching patterns accurately.
I appreciate how servo motors offer precise control over these aspects.
They can easily halt the sewing process at the exact moment without lag, which is beneficial for detailed work.
In contrast, induction motors may have a delayed response, affecting the quality of a seam.
Electrical Considerations for Sewing Machines
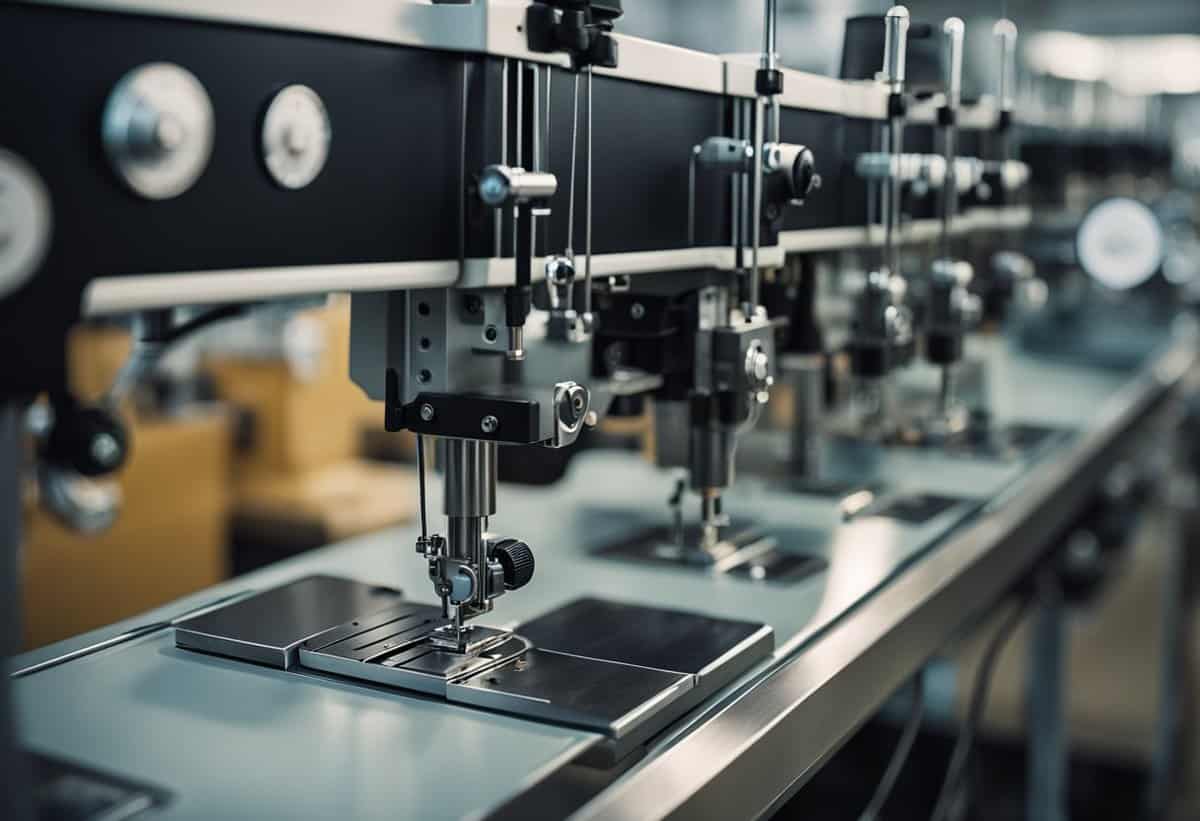
When selecting motors for industrial sewing machines, understanding electrical requirements is crucial. This includes voltage and power needs as well as concerns about electromagnetic interference. These factors greatly impact performance and reliability.
Voltage and Power Requirements
Industrial sewing machines typically operate on specific voltage levels that ensure efficient performance.
Most machines are designed to work with standard voltages, such as 110V or 220V. The choice of voltage affects the machine’s power efficiency and overall effectiveness.
Power requirements can vary, but many industrial sewing machines use around 100 to 500 watts, depending on their application.
For heavy-duty models, the wattage may go even higher, ensuring they can handle thicker materials without losing power.
Using the wrong voltage can lead to poor performance or damage.
It’s vital for operators to check the voltage ratings of their machines and ensure they match their power sources.
Electromagnetic Interference Concerns
Electromagnetic interference (EMI) is an important consideration when using electric motors in sewing machines.
Induction motors, while popular in other applications, can produce significant EMI, which can disrupt electronic sewing components.
Servo motors, often preferred for industrial sewing machines, tend to generate less EMI.
This is important because reduced interference leads to better functionality of electronic features, such as speed control and stitch adjustments.
Minimizing EMI helps maintain the accuracy and quality of sewing operations.
Comparison with Other Motor Types
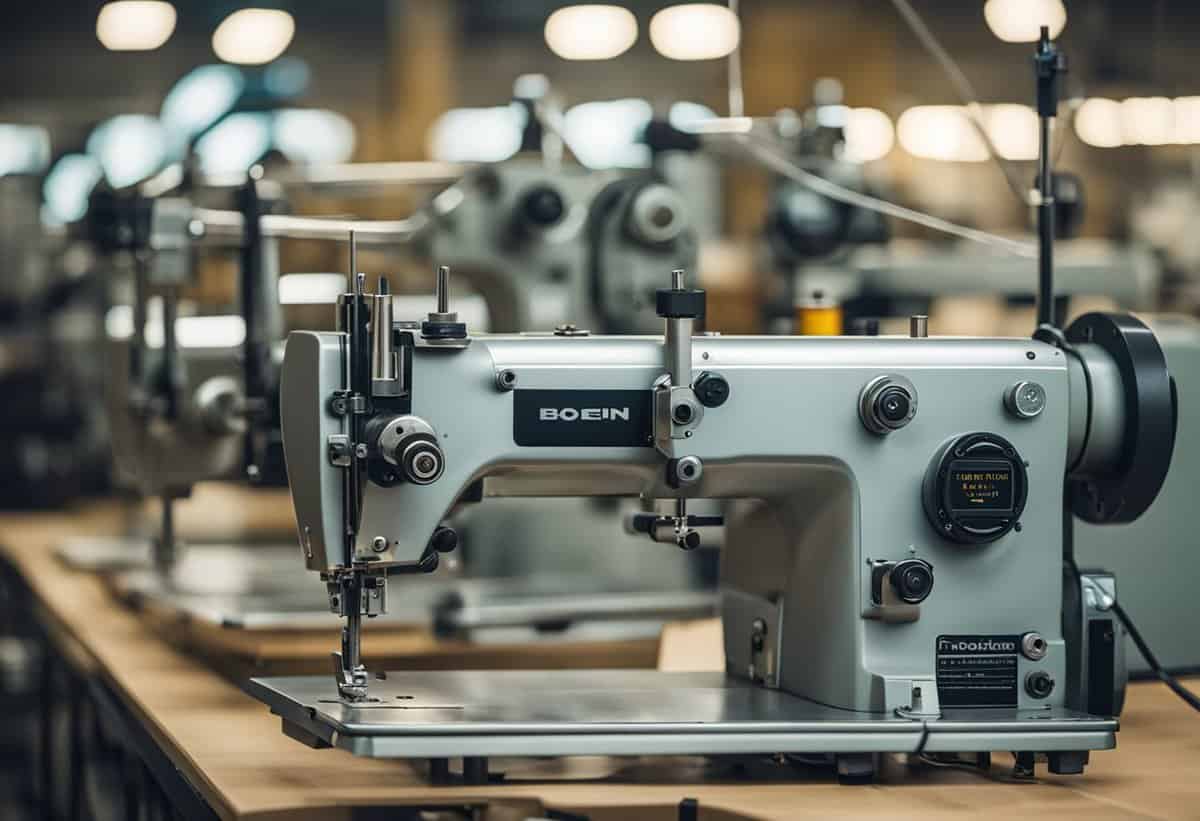
In my exploration of industrial sewing machines, I often find that the choice of motor type is crucial. Induction motors are not favored for these machines, primarily due to their limitations in control and efficiency. Here, I will compare the most commonly used alternatives: servo motors and clutch motors.
Servo Motors
I appreciate the advantages of servo motors in industrial sewing machines.
They offer precise control over speed and position through a closed-loop system. This means the machine responds effectively to the operator’s inputs via the foot pedal, allowing for smooth and accurate stitching.
The energy efficiency of servo motors stands out. They use only the power needed for the operation, reducing overall energy consumption.
Additionally, servo motors operate quietly, which is a significant benefit in environments where noise can be distracting.
Clutch Motors
Clutch motors serve a different purpose in industrial sewing. These motors engage and disengage using a clutch mechanism, providing good control over sewing speed.
I find that they allow for high power output, making them suitable for heavy-duty tasks.
However, clutch motors require more maintenance compared to servo motors.
The wear and tear on parts can increase operational costs and downtime. Despite this, their reliability in high-volume production settings keeps them relevant in the industry.
Cost and Maintenance Factors
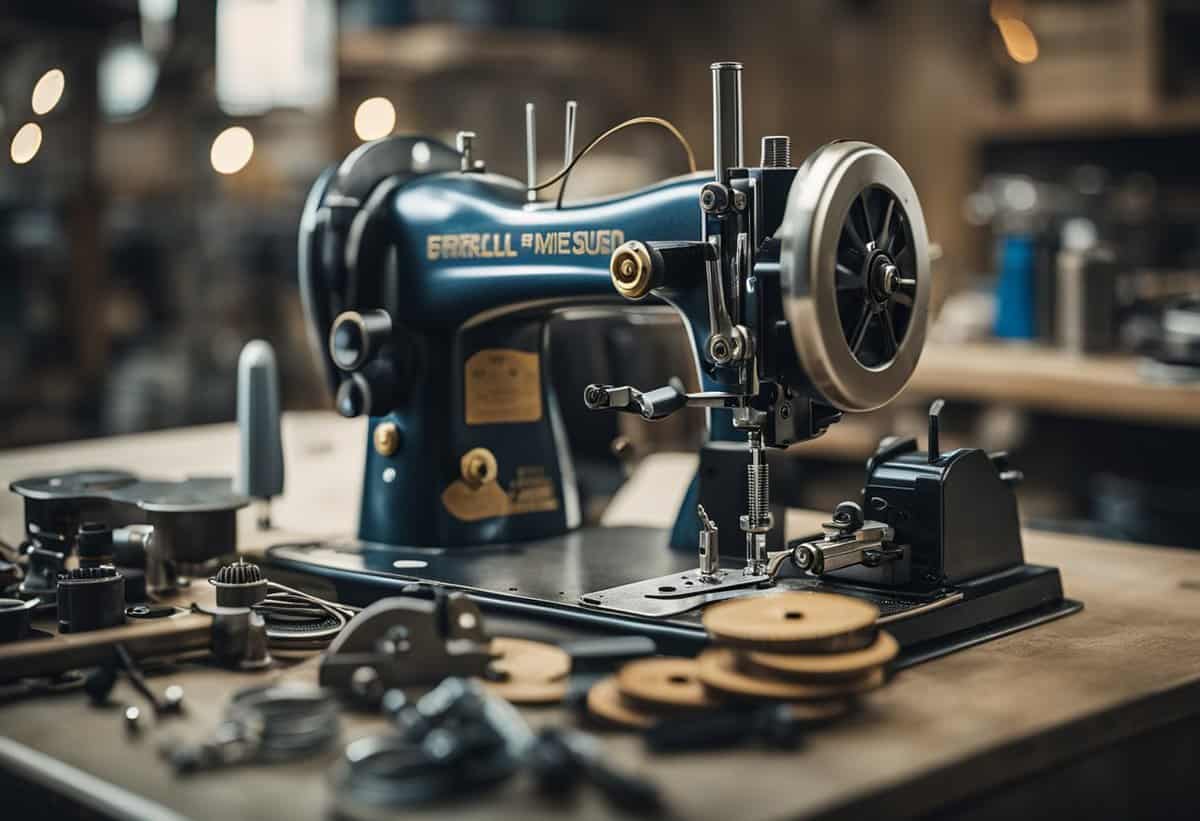
When I think about industrial sewing machines, the cost and maintenance aspects are crucial. These factors significantly influence the choice of motors used in these machines.
Initial Investment
The initial cost of industrial sewing machines can vary widely.
Most machines range from a few hundred to several thousand dollars.
For example, a entry-level machine may start around $1,000, while those with advanced features might cost between $1,000 and $2,500.
Servo motors, which are often used in these machines, tend to be more expensive than induction motors.
This higher upfront cost is justified by their efficiency and performance. They provide precise control, reducing material waste.
This can save money in the long run, even if the initial outlay is higher.
Long-Term Maintenance
Maintenance expenses also play a significant role in decision-making.
Servo motors and clutch motors usually require less frequent servicing compared to induction motors.
For instance, induction motors can run hot and may need more repairs over time.
Because servo motors are less complex, they often incur lower repair costs.
These motors also have longer lifespans due to fewer moving parts. This reliability translates into reduced downtime, which is essential for operations that rely on efficiency.
Innovation and Future Trends
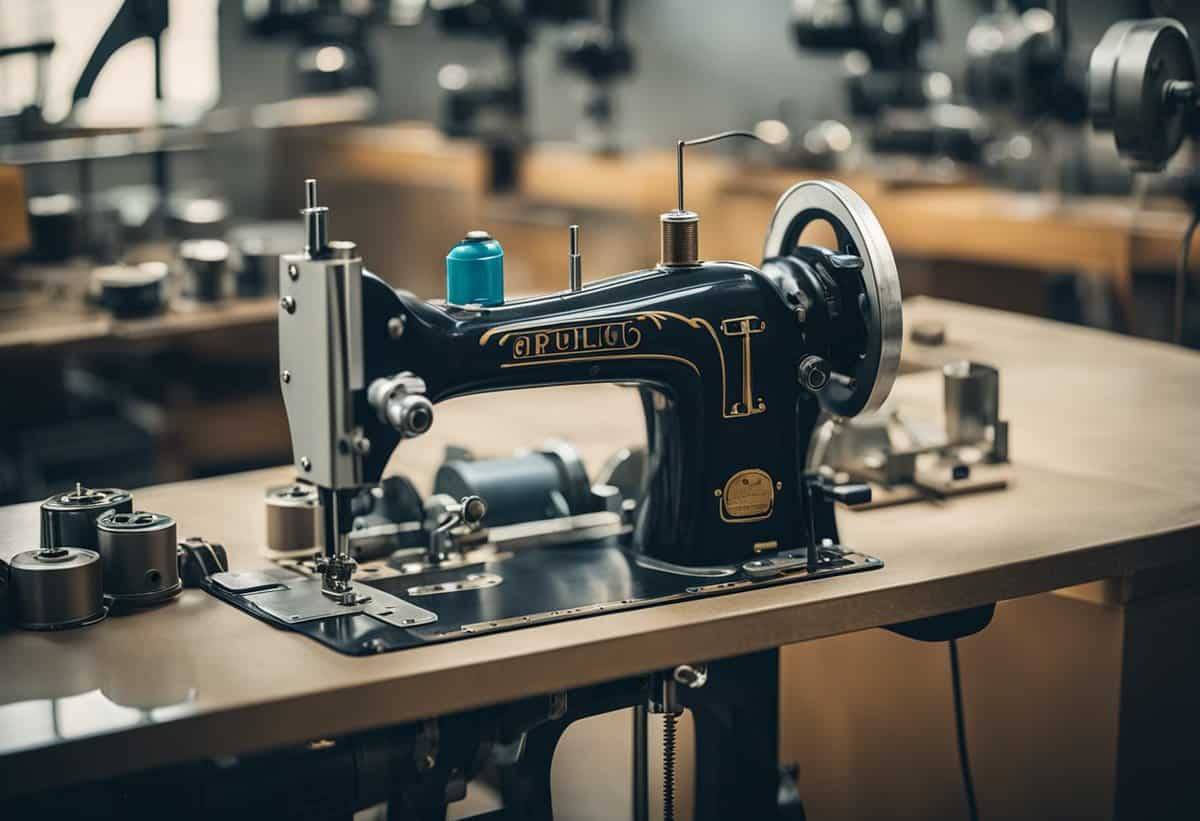
The landscape of industrial sewing machines is evolving rapidly. This evolution is driven by advancements in technology and a strong focus on sustainability.
I find that these trends are shaping the future of sewing machines and their motors in significant ways.
Emerging Technologies
New technologies are transforming how industrial sewing machines operate.
For instance, servo motors have become popular replacements for induction motors.
They offer precise control and energy efficiency, allowing for faster and more accurate stitching.
Additionally, smart sewing machines feature integrated sensors that monitor performance in real time.
These features enable quick adjustments, enhancing productivity and reducing material waste.
Automation is also growing, with machines capable of self-adjusting tension settings or applying stitches based on fabric type, providing flexibility.
Machine learning can further optimize performance, leading to innovations that ensure higher quality output over time.
Sustainability in Motor Design
Sustainability is gaining importance in the design of industrial sewing motors.
I see a shift toward using materials and technologies that reduce environmental impact.
For example, manufacturers are exploring energy-efficient options that consume less power than traditional induction motors.
Furthermore, companies are beginning to embrace the use of recyclable materials in their production processes.
Lightweight designs help minimize energy use during operation.
This focus on sustainability not only addresses environmental concerns but also can appeal to consumers who prioritize eco-friendly practices.
By adopting sustainable motor designs, the industry is moving toward a more responsible future.
FAQs:
Why do industrial sewing machines not use induction motors?
Industrial sewing machines primarily avoid induction motors due to their limited ability to provide precise speed control and torque at low speeds. Sewing operations often require high precision and variable speeds, which are better achieved with clutch or servo motors.
What types of motors are commonly used in industrial sewing machines?
Industrial sewing machines typically use servo motors or clutch motors. Servo motors are favored for their energy efficiency, quiet operation, and precise control, while clutch motors are robust and suitable for heavy-duty tasks but consume more energy.
Are induction motors less efficient than servo motors in sewing machines?
Yes, induction motors are less efficient in this context because they lack the dynamic control necessary for sewing applications. Servo motors, in contrast, adjust speed and torque efficiently, reducing energy consumption and ensuring smoother operation.
What are the key performance factors considered when choosing motors for sewing machines?
The primary factors include precision in speed control, torque consistency, energy efficiency, noise levels, and suitability for the specific sewing tasks. Servo motors excel in most of these aspects, making them ideal for industrial sewing machines.
Why are induction motors more commonly used in other industrial applications?
Induction motors are reliable, low-maintenance, and cost-effective for applications requiring consistent high-speed operation. However, they are not suited for tasks needing frequent speed variations or high precision, like sewing.
Can induction motors ever be used in industrial sewing machines?
While theoretically possible, induction motors would require complex additional systems for speed control, making them less practical and cost-efficient compared to servo motors.